Understanding Steel Prices and Their Impact on Machinery Costs
In the world of industrial machinery, one of the most critical factors influencing costs is the price of steel. Steel is a fundamental component in manufacturing a wide range of equipment, from construction machinery to factory automation systems. Fluctuations in steel prices can significantly impact the overall cost of these machines. This article explores how steel prices affect machinery costs and offers insights into navigating these changes.
The Role of Steel in Machinery Manufacturing
Steel is prized for its durability, strength, and versatility, making it an essential material in machinery manufacturing. From the frame of a forklift to the intricate parts of a CNC machine, steel’s presence is ubiquitous. Given its importance, any change in steel prices can ripple through the machinery market, affecting both manufacturers and buyers.
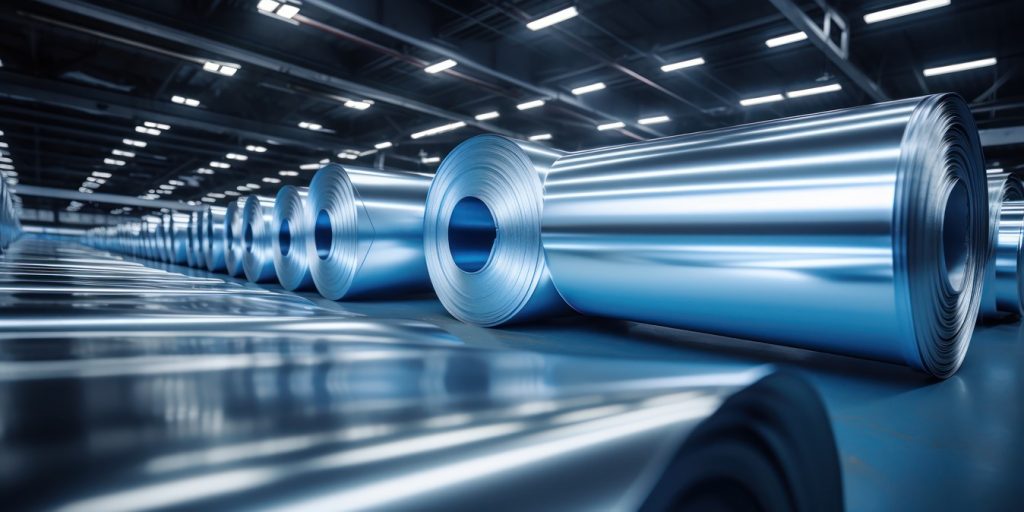
Factors Influencing Steel Prices
Several factors can drive the fluctuation of steel prices, including:
Supply and Demand: The basic economic principle where increased demand or reduced supply can lead to higher prices.
Raw Material Costs: The prices of raw materials used in steel production, such as iron ore and coal, directly impact steel prices.
Energy Costs: Steel production is energy-intensive, so changes in energy costs can influence steel prices.
Global Trade Policies: Tariffs, trade agreements, and other international trade policies can affect the cost and availability of steel.
Economic Conditions: The overall economic environment can influence industrial activity and thus the demand for steel.
Impact of Steel Prices on Machinery Costs
Increased Production Costs: Higher steel prices mean increased production costs for manufacturers. These costs are often passed down the supply chain, leading to higher prices for machinery.
Budget Adjustments: Buyers may need to adjust their budgets to account for increased machinery costs, which can affect project planning and financial forecasting.
Market Competitiveness: Manufacturers who can source steel at lower costs may offer more competitive pricing, influencing market dynamics.
Innovation and Efficiency: In response to rising steel prices, manufacturers might invest in more efficient production techniques or alternative materials to control costs.
Strategies to Mitigate the Impact of Steel Price Fluctuations
Long-term Contracts: Securing long-term contracts with steel suppliers can help stabilize costs and protect against sudden price hikes.
Diversification: Sourcing steel from multiple suppliers or regions can reduce dependency on a single source and mitigate risk.
Inventory Management: Maintaining an optimal level of steel inventory can buffer against price fluctuations.
Alternative Materials: Exploring alternative materials or composites that can replace steel in certain applications without compromising quality.
Technology Investment: Investing in technology to improve production efficiency and reduce waste can help offset higher material costs.
Why Consulting Professionals is Crucial
Given the complexities involved in machinery manufacturing and the volatility of steel prices, consulting with industry professionals is essential. Professionals can provide insights into market trends, offer strategic purchasing advice, and help in selecting the right equipment that meets both budgetary constraints and operational requirements.
In conclusion, the price of steel plays a pivotal role in determining the cost of machinery. Understanding the factors that influence steel prices and implementing strategies to manage these fluctuations can help businesses make informed purchasing decisions. At Top Machineries & Equipments, we are committed to helping our clients navigate these challenges by offering expert advice and high-quality machinery tailored to their specific needs.
For more information on how to choose the right machinery for your industry, visit Top Machineries & Equipments.
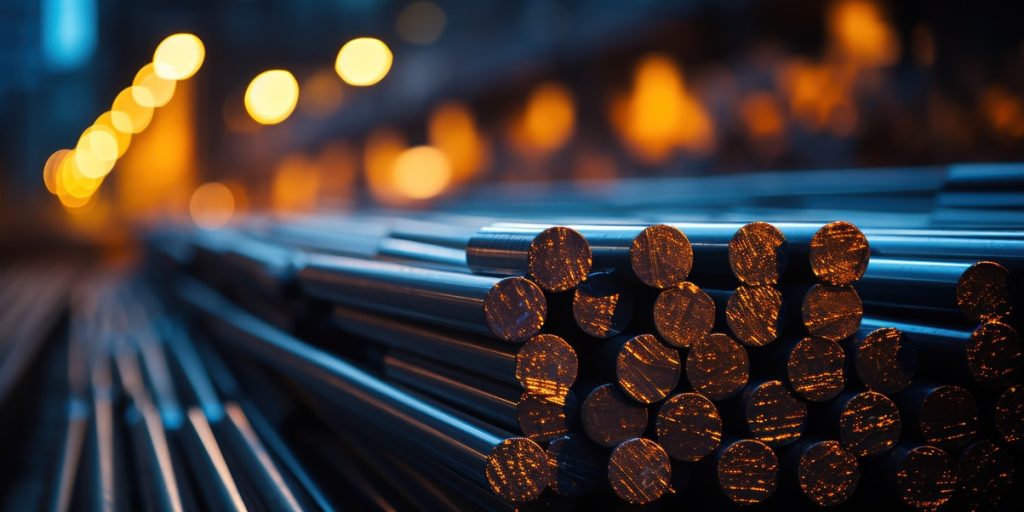
0 Comments